Artikel:
Lean Management – Ziele, Grundbegriffe, Methoden und Vorteile
Während Lean Management in vielen industriellen Großbetrieben bereits länger eine relevante Thematik ist, war Lean im Mittelstand lange Zeit nur ein dubioser Begriff. Inzwischen gewinnt der Lean Gedanke jedoch auch kleineren und mittleren Unternehmen zunehmend an Bedeutung und das zu Recht. Dank der effizienten Gestaltung der Wertschöpfungskette steigert diese Art des Wirtschaftens schließlich die Gesamtleistung eines Unternehmens um ein Vielfaches.
Dieser Artikel gibt eine Lean Management Definition, geht auf die Frage “Was ist Lean Management“ ein, beleuchtet Vorteile und Lean Management Nachteile und liefert einen Einblick in die Lean Management Methode anhand eines Projektbeispiels inklusive Kennzahlen.
LEAN MANAGEMENT EINFÜHRUNG MEISTERN
LEAN MANAGEMENT EINFÜHRUNG MEISTERN
– HIER EINBLICK ERHALTEN
Vorteile und Nachteile Lean Management
Die Implementierung von Lean Management bringt diverse Vorteile, aber auch anfänglich potenzielle Nachteile mit sich. Nachfolgend werden die gängigsten aufgelistet und näher erklärt.
Nachteile Lean Management
Ein potenzieller Nachteil von Lean Management besteht darin, dass die Einführung dieses Ansatzes mit erheblichem Zeitaufwand verbunden sein kann und häufig auf Widerstände im Unternehmen stößt. Die Implementierung erfordert in vielen Fällen eine tiefgreifende Veränderung der Unternehmenskultur, was wiederum umfassende Ressourcen und ein hohes Maß an Geduld erfordert. Zusätzlich dazu müssen Mitarbeitende geschult werden, um die Lean-Prinzipien zu verstehen und umzusetzen, was Zeit und Investitionen erfordert. Dieser Transformationsprozess kann anfänglich als Herausforderung wahrgenommen werden, sollte jedoch als eine notwendige Investition betrachtet werden, um die langfristigen Vorteile von Lean Management zu realisieren.
Vorteile Lean Management
Richtig eingesetzt und durchgeführt, überwiegen die Vorteile von Lean Management klar. Hierzu gehören vor allem die folgenden:
- Höhere Produktivität: Durch die Reduzierung von Verschwendung und ineffizienten Prozessen optimiert Lean Management den Arbeitsablauf. Das Ergebnis ist eine gesteigerte Produktivität, da Ressourcen effektiver genutzt und Engpässe minimiert werden können.
- Gesteigerte Qualität: Lean Management legt großen Wert auf Fehlervermeidung und kontinuierliche Verbesserung. Dies führt zu einer konstanten Qualitätssteigerung, da Defekte frühzeitig erkannt und eliminiert werden, bevor sie sich auswirken können.
- Schnellere Lieferperformance: Die Umstellung auf Just-in-Time-Prinzipien und kontinuierlichen Fluss in der Produktion ermöglicht eine schnellere Lieferung von Produkten und Dienstleistungen. Dies führt zu kürzeren Durchlaufzeiten und erhöhter Kundenzufriedenheit.
- Kostenersparnis: Die Eliminierung von Verschwendung in allen Bereichen eines Unternehmens führt zu deutlichen Kosteneinsparungen. Weniger Lagerhaltung, geringere Ausschussraten und optimierte Prozesse tragen zur finanziellen Effizienz bei.
- Mitarbeiterentlastung: Lean Management fördert die Einbeziehung und Beteiligung der Mitarbeiter an kontinuierlichen Verbesserungsprozessen. Indem Barrieren für effizientes Arbeiten abgebaut werden, erfahren Mitarbeiter weniger Frustration und Stress, was zu höherer Zufriedenheit führt.
- Ressourcenschonung: Die Fokussierung auf effiziente Prozesse und Ressourcennutzung reduziert den Verbrauch von Rohstoffen, Energie und anderen Ressourcen. Dies trägt zur Nachhaltigkeit bei und minimiert die ökologische Belastung.
Alle diese Punkte schlagen sich in mehr Umsatz, einer höheren Kundenzufriedenheit und einer gesteigerten Wettbewerbsfähigkeit nieder.
Was ist Lean Management?
Die Frage nach einer Lean Management Definition lässt sich am Besten direkt aus dem Unternehmenskontext heraus beantworten: Jedes Unternehmen ist auf Kunden angewiesen. Somit ist jede Führungskraft angehalten in ihrem Verantwortungsbereich für ein hohes Maß an Kundenorientierung zu sorgen. In erster Linie zeigen sich die Kundenwünsche in folgenden drei Kernkategorien: Eine hohe Produktqualität, eine gute Lieferperformance und minimale Kosten. Das wirkt zunächst nur schwer erfüllbar, ist aber durch die Implementierung der geeigneten Lean Prinzipien erreichbar.
Das Zufriedenstellen der Kunden hat im Lean Management die oberste Priorität. Der Kerngedanke spiegelt sich im Grunde in der folgenden Frage wider: Wie können wir die Kundenanforderungen in Bezug auf das Produkt bzw. die Dienstleistung mit einem Minimum an Verschwendung erfüllen?
Folglich geht es also darum, sämtliche Aktivitäten in einer Organisation so auszurichten, dass die Kundenerwartungen in Bezug auf Qualität, Kosten und Lieferperformance erfüllt werden. Hierfür müssen unnötige Zeitverluste in Arbeitsprozessen als Verschwendung betrachtet und mittels verschiedener Tools sichtbar gemacht sowie vermieden werden.
ZIELE & VORTEILE VON LEAN MANAGEMENT ENTDECKEN
ZIELE & VORTEILE VON LEAN ENTDECKEN
Wie die Lean Management Methode funktioniert
Viele sprechen von der Lean Management Methode oder von einem Set von Lean Management Methoden. Aber diese Bezeichnung ist schwierig – Lean Management ist viel mehr als eine Methode – es ist ein Set von Tools, das richtig eingesetzt, zu einer Steigerung des Umsatzes, einer erhöhten Kundenzufriedenheit und einer gesteigerten Wettbewerbsfähigkeit führt. Wichtige Elemente werden im folgenden anhand von einem Kundenbeispiel näher erläutert.
Qualität, Kosten und Liefertreue
Hauptziele eines jeden Unternehmens sind es die Qualität und Liefertreue möglichst hoch zu halten und zeitgleich die Kosten zu senken. Diese Ziele stehen in Konkurrenz zueinander. Lean schafft es Qualität, Kosten und Liefertreue ohne Kompromisse zu steigern.
Im Rahmen der Ist-Analyse bei unserem Kunden Mebrutec wurden diese Kennzahlen ermittelt: Es konnte eine Liefertreue von 59,07 % festgestellt werden. Diese niedrige Zahl spiegelt die langen stark schwankenden Durchlaufzeiten, die ineffizienten und unstrukturierten Prozesse und hohe Bestände im Unternehmen wider. Im Laufe des Projekts wird zudem erstmals die Kennzahl Qualität der Produktion aufgenommen. Diese wird anhand von Qualitätsfehlern gemessen und wird in interne und externe Qualität unterteilt. Die interne Qualität bezieht sich auf die Fehler im Laufe des Produktionsprozesses. Die externe Qualität berücksichtigt dabei Reklamationen durch den Kunden. Da die Datenaufnahme erst kürzlich eingeführt wurde, existieren hierzu noch keine aussagekräftigen Ergebnisse.
Unter anderem die niedrige Liefertreue, fehlende Qualitätsdaten sowie die nicht vorhandene Wertstromorientierung mögen den Eindruck vermitteln, dass es dem Kunden an Konkurrenzfähigkeit mangelt, doch tatsächlich ist das Gegenteil der Fall. Die herausgearbeitete Transparenz durch Zahlen, Daten und Fakten spiegelt das hohe Potenzial wider und zeugt von einer zukunftsorientierten Perspektive.
Prozesse aus der Kundenperspektive betrachten
Erst durch die Bewertung der Prozesse aus der Kundenbrille, lässt sich klar identifizieren, welche Prozesse wertschöpfend sind und welche Verschwendung darstellen. Das übergeordnete Ziel von Lean Management ist aus der Unternehmensperspektive aber nicht nur die externe Kundenzufriedenheit, sondern auch die interne. Unter internen Kunden versteht man die eigene Belegschaft. Das Team über alle Ebenen hinweg, von der Geschäftsführung über die Managementebene bis hin zum Ort der eigentlichen Wertschöpfung, dem Fertigungsbereich.
Die Betrachtung der Prozesse und der Wertschöpfungskette aus der Kundenperspektive ist einer der wichtigsten Ansätze der Lean Philosophie. Die Unternehmensprozesse müssen so ausgerichtet sein, dass die Produkte den Kundenanforderungen hinsichtlich Qualität, Kosten und Liefertreue entsprechen. Die einzelnen Aspekte der Ist-Analyse werden deswegen ebenfalls aus der Kundenperspektive betrachtet. So wird unter anderem die Effizienz einzelner Arbeitsschritte genau gemessen. Die Ergebnisse werden dafür genutzt, um im Nachhinein ineffiziente Prozesse zu eliminieren bzw. zu optimieren. Dies sorgt wiederum für eine Entlastung der Mitarbeitenden, eine kürzere Produktionszeit, bessere Lieferzeiten und resultiert in zufriedeneren Kunden.
Wertschöpfung vs. Verschwendung
Erst durch die Unterscheidung von Wertschöpfung und Verschwendung lässt sich das immense Potenzial in Unternehmen identifizieren. Die Tätigkeiten eines Arbeitsprozesses setzen sich aus verschiedenen Zeitanteilen zusammen. Wertschöpfende Tätigkeiten, notwendige und unnötige Verschwendungen (Zeitverluste). Steigender Wettbewerbsdruck zwingt Unternehmen zu einer permanenten Optimierung der Leistungserstellung. In diesem Zusammenhang stellt die Wertschöpfungszeit – die Zeit, in der eine Person oder Maschine aktiv auf ein konkretes Ergebnis bzw. Ziel hinarbeitet – eine wesentliche Kenngröße dar. Die Wertschöpfungszeit ist also die reine Bearbeitungszeit, die einem Produkt oder einer Dienstleistung einen Wertzuwachs erbringt.
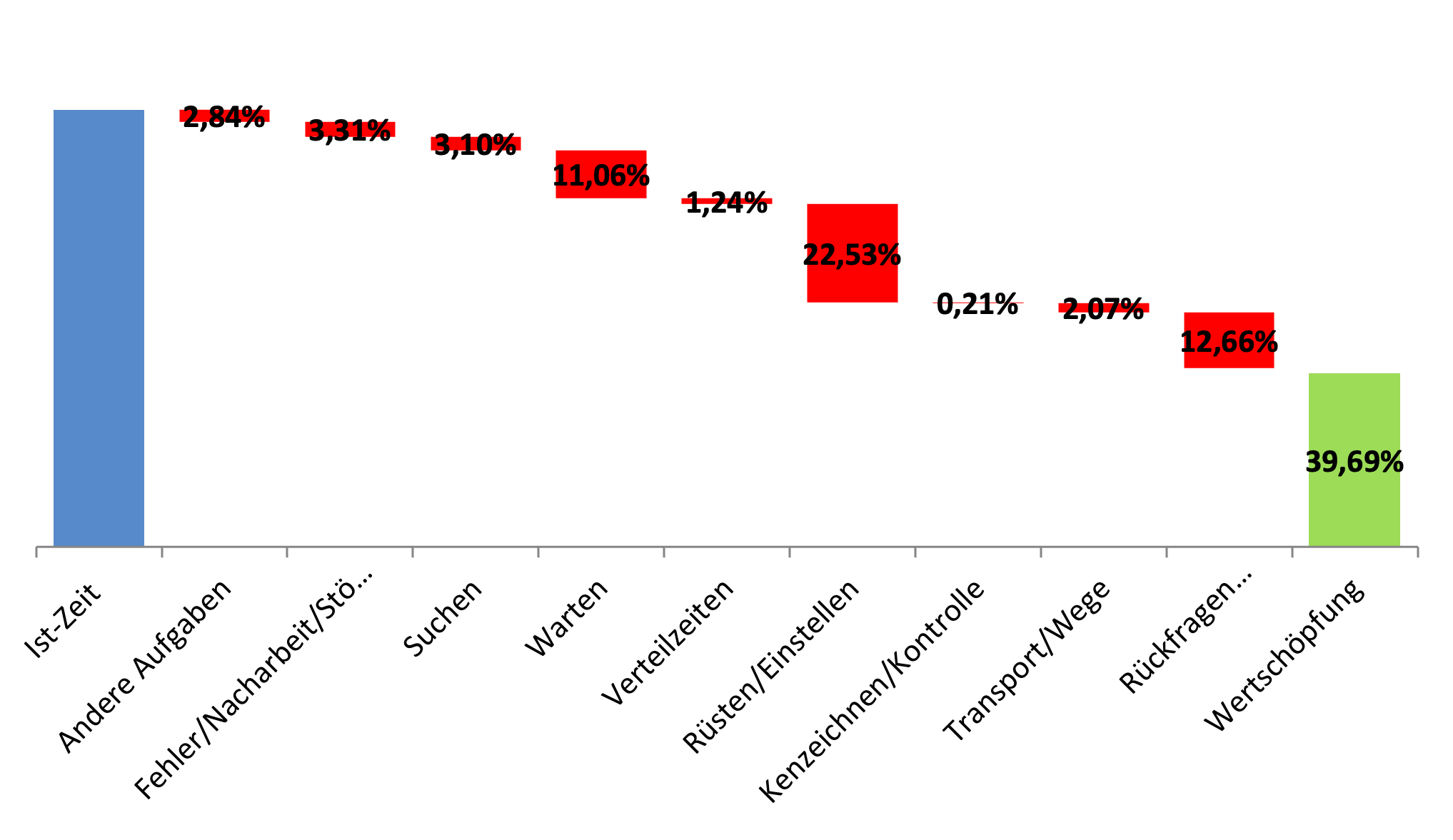
Unsere Analyse zeigt, dass nur 39,69 % der Gesamtarbeitszeit der Mebrutec Mitarbeiter wertschöpfend genutzt werden. Die Mitarbeiter beschäftigen sich circa 60 Prozent ihrer Arbeitszeit mit Tätigkeiten, die aus Kundenperspektive nicht zum Mehrwert des Produktes beitragen. Dies liegt jedoch nicht, wie man zunächst vermuten könnte, an unmotivierten oder gar faulen Mitarbeitern, sondern schlichtweg an der fehlenden Wertschöpfungsorientierung des Unternehmens.
Drei große Zeitfresser fielen bei der Analyse auf: 22,53 % der Arbeitszeit verbringen die Mitarbeitenden im Dreh- und Fräsbereich mit dem Rüsten und Einstellen der Maschinen. Während dieser Zeit können die Maschinen nicht produktiv genutzt und keine Produkte gefertigt werden. Der Punkt Rückfragen und Kommunikation bildet mit 12,66 % den zweitgrößten Zeitfresser. Fehlende Strukturen und nicht standardisierte Arbeitsplätze und -prozesse fördern eine situative Kommunikationskultur unter den Mitarbeitenden und der Geschäftsführung. Die hohe Anzahl an täglichen Rücksprachen hält Mitarbeitende von ihrer Arbeit oft unnötig ab.
Außerdem verbringen die Mitarbeitenden 11,06 % ihrer Arbeitszeit mit Warten. Entweder überwachen sie die Maschinen oder warten auf Werkzeug, Materialnachschub, Teile oder auf den nächsten Schritt der Weiterverarbeitung. Vor allem das Warten auf Material verzögert den Fertigungsprozess erheblich.
Die 7 Verschwendungsarten
Die unnötigen Zeitverluste, die es zu vermeiden gilt, werden in der klassischen Lehre in sieben Arten der Verschwendung unterteilt. Hierzu gehören Materialbewegungen (das unnötige Transportieren von Materialien), Bestände (unnötige Bestände von End- und Zwischenprodukten), sonstige Bewegungen (unnötige Bewegungen von Mensch und Maschinen), Wartezeiten (geplantes und ungeplantes Warten), Überproduktion (Produkte ohne Kundenanforderung), Überarbeitung (unnötig aufwändige Bearbeitungen) und Fehler (Ausschuss, Nacharbeiten oder Korrekturen).
Ein einfaches Beispiel soll eine Verschwendungsart kurz skizzieren: Wenn interne Transportwege nicht aufeinander abgestimmt sind, entstehen überflüssige Wartezeiten zwischen Prozessschritten. Wartezeiten, die das Ausliefern eines Produkts im Endeffekt unnötig verlängern und Kunden, die eigentlich im Mittelpunkt stehen sollten, wegen der langen Lieferzeit verärgern. Im schlimmsten Fall führt dies nicht nur zu Verärgerung, sondern auch dazu, dass die Kunden woanders bestellen. Mittels Wertstromanalyse können diese nicht optimalen Transportwege aufgedeckt werden und im Rahmen von Workshops Potenziale ausgeschöpft werden, um schnellere Lieferzeiten zu erzielen.
Durchlaufzeit
Durch die kontinuierliche Eliminierung der Verschwendung in Arbeitsprozessen, lässt sich die Durchlaufzeit extrem reduzieren. Stark schwankende Durchlaufzeiten ist eines der größten Probleme in der Fertigung. Um diese zu optimieren, analysierten wir in einem Kundenprojekt zunächst die Faktoren, die maßgeblich die Durchlaufzeit beeinflussen.
Neben hohen Liege- und Wartezeiten des Materials kann eine hohe Durchlaufzeit auch aus ineffizienten Prozessen resultieren. Hierbei können sich Engpässe sowohl an den Maschinen und Anlagen, wie auch beim Mitarbeitenden zeigen. Um dies im Detail beurteilen zu können, wurden bei Mebrutec sowohl die Maschinenauslastung gemessen als auch Tätigkeitsstruktur- und Bewegungsanalysen der Mitarbeiter durchgeführt.
Die Maschinenauslastung zeigt, wie viel Prozent der gesamten Arbeitszeit an der Maschine zum Produzieren und Fertigen der Teile genutzt wird. Die Auswertung dieser Kennzahl ergab einen Wert von 5,26 %. Das heißt, dass die Maschinen während ca. 95 % der Gesamtarbeitszeit stillstehen. Die Maschinenauslastung stellt also für Mebrutec keinen Engpass, sondern vielmehr ein Potenzial dar. Sollte sich die Auftragslage deutlich verbessern, hätte Mebrutec genug maschinelle Kapazitäten, um zusätzliche Aufträge zu stemmen.
Fazit
Toyota legte die Grundlage des Lean Gedankens und zielte darauf ab, Prozesse zu eliminieren, die für das Endprodukt keinen Wert haben. Eine signifikante Verbesserung der Produktivität, eine bessere Lieferperformance und verringerte Kosten waren die Folge. Seither hat sich der Lean Gedanke in zahlreichen Branchen verbreitet.
Um den Lean-Gedanken in seiner Breite vollständig, erfolgreich und nachhaltig etablieren zu können, ist es entscheidend, die Mitarbeitenden vom Mitmachen zu überzeugen. Nur eine gemeinsame Verantwortung führt zum Ziel. Die Mitarbeitenden mit ins Boot zu holen und den Willen zur Veränderung in ihnen zu wecken, ist allerdings nicht mal so eben gemacht. Mitarbeitermitnahme und Change Management sind die richtigen Grundbegriffe, um die Belegschaft in den Veränderungsprozess von Beginn an mit einzubinden.
Einen tieferen Einblick in die typischen Fehler und Probleme bei der Implementierung von Lean Management Methoden zeigt der Beitrag: 6 Gründe warum die Lean Management Implementierung scheitert.
Lesen Sie weitere spannende Artikel:
ERP – drei typische Fehler bei der Einführung
ERP - Drei Typische Fehler bei der Einführung Wer ERP im Mittelstand oder anderen Unternehmensgrößen einführt, ohne die Prozesse vorher nach Lean ausgerichtet zu haben, steht unweigerlich vor Problemen mit zum Teil verheerenden Auswirkungen für einzelne Abteilungen...
Was sind ERP-Systeme
Artikel:ERP-Systeme verstehenViele mittelständische Unternehmen wollen Prozesse effizienter gestalten und digitalisieren. Um wettbewerbsfähig zu bleiben und erfolgreich zu expandieren, benötigen Mittelständler effiziente Tools und Systeme. Dabei sehen sie sich...
Wissenstransfer und Suchzeitoptimierung im Mittelstand
Artikel:Wissenstransfer und Suchzeitoptimierung im Mittelstand Für viele Geschäftsführer gehört die folgende Situation zum Tagesgeschäft: Unbewusst werden durch die Kosten, die aufgrund von typischen Betriebsproblemen entstehen, Investmentanträge für mehrere Tausende...